Why Amazon is swapping battery-electric forklifts for hydrogen fuel cells
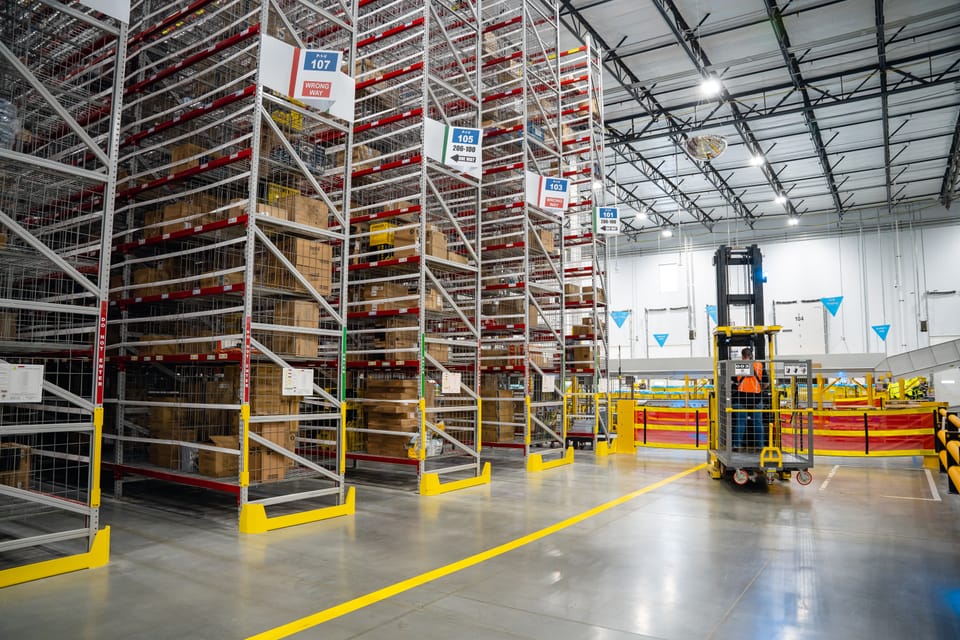
While much of the world is focused on deploying battery-electric vehicles (BEVs) to decarbonise mobility, Amazon is swapping its electric forklift batteries for hydrogen fuel cells. What are the drivers behind this strategic decision – and should other companies follow?
Hydrogen solutions provider Plug Power installed the first electrolyser at an Amazon fulfilment centre in Colorado in December. The machine uses electricity and water to produce hydrogen, which will fuel 400 fuel cell-powered forklift trucks at the site.
Amazon has long been a user of Crown electric forklifts, which are equipped either with lead-acid or lithium-ion batteries. But Plug has now deployed more than 17,000 fuel cells to replace these forklift batteries in more than 80 Amazon fulfilment centres in North America.
This is a clear strategy shift that may raise some eyebrows. Amazon says with its electrolyser will make use of surplus, locally generated renewable energy, but why not use the same excess power to charge its existing electric forklifts, which are already zero emissions?
Benefits of hydrogen
Any company operating a fleet of vehicles is likely to consider both technologies for decarbonisation. Each presents benefits and downsides, and until recently, appeared equally likely to replace thermal engines in industrial vehicles.
Hydrogen fuel cell engines work in a similar way to diesel or engines in that they have to be refilled – with hydrogen as a fuel. When combined with oxygen, it creates electricity, with water vapour as a byproduct. Hydrogen fuel cell cars can run 300 to 400 miles on a single tank, which is refilled in minutes. In comparison, the average range of an electric car today is 227 miles – and batteries can take up to 40 hours to charge.
Amazon and Plug declined to comment for this article, but speed of refilling has previously been mentioned by Plug CEO Andy Marsh as one of the main reasons why anyone, including Amazon, would want to swap batteries for fuel cells in forklifts. By reducing charging times, this type of vehicle cuts labour cost and keeps warehouses working around the clock.
Growth of hydrogen production and infrastructure
Most of the hydrogen used in fuel cell vehicles today is produced off site and transported from specialised storage facilities, but Amazon’s Colorado fulfilment centre will now be supplied by on-site production.
Electrolysers use high-voltage current to split the hydrogen and oxygen molecules in water, so they consume large amounts of electricity. The Colorado is powered by 6 MW of solar energy coming from 17,280 rooftop panels, and Plug says the electrolyser there will be partly powered by excess solar energy – though reports suggest it will also be plugged into the local grid, which still gets much of its power from coal.
It’s worth noting that hydrogen is only a green fuel if it is made using water and renewable electricity – creating so-called ‘green hydrogen’. Other classifications include blue hydrogen (made from natural gas with carbon capture – the cheapest type today) and grey hydrogen (made from fossil fuels without abatement).
Green hydrogen is currently the most expensive type to produce, at US$4.5-US$12 per kilo – compared to US$0.98-US$2.93 for grey hydrogen. BloombergNEF expects this trend to reverse by 2030 as fossil fuels become more expensive than renewables, but experts warn that producing large amounts of green hydrogen would require much more renewable power than is available.
Additionally, hydrogen is a highly volatile and flammable molecule that needs to be compressed and stored in precise conditions, either as a gas in high-pressure tanks or in liquid form at cryogenic temperatures.
This complicates the development of refilling infrastructure, creating another obstacle in the growth of the hydrogen market: At the end of 2022, there were 2.7 million public electric vehicle charging points worldwide, and just 814 hydrogen refuelling stations.
The hydrogen business case for Amazon
Critics could argue that the electricity used to make hydrogen through the electrolyser and then refill fuel cell forklifts could be used more directly to charge battery-electric forklifts instead. But aside from the added productivity gained by shorter charging times, this is also a long-term, strategic investment for Amazon.
The trillion-dollar tech giant launched a US$2 billion Climate Pledge Fund in 2020, through which it has invested in 18 carbon technology companies providing decarbonisation solutions including electric vehicles and battery recycling and hydrogen.
Additionally, its offtake agreement with Plug Power also includes a US$2.1 billion stock option – so it is in Amazon’s (financial) interest to support the development of the hydrogen economy.
The company is in a race to become net zero by 2040, and to do so it is leveraging all the technologies at its disposal: to date, it has also deployed more than 10,000 battery-electric vans for last-mile deliveries across the US.
Amazon has the resources to invest in various decarbonisation technologies, and its complex logistics network, with many different types of vehicles, allows it to test different use cases for both hydrogen and battery-electric solutions. But for most other companies, decarbonising the fleet means committing to one or the other.
Choosing between BEVs and hydrogen fuel cells
Like most other sustainability decisions, fleet decarbonisation technologies should be chosen on a case-by-case basis, based on several criteria, among which:
- Vehicle range: the longer the range, the better the hydrogen business case.
- Availability of renewable energy: both batteries and fuel cells require renewable electricity to be a truly green solution, but hydrogen production is far less efficient than battery charging, so it requires copious amounts of excess generation.
- Infrastructure: wherever your vehicles operate, chances are there are more electric charging stations than hydrogen refuelling stations, but certain regions are investing heavily in hydrogen infrastructure. The IEA Hydrogen Production and Infrastructure Database is a great starting point to understand the future landscape.
- Cost: a recent study comparing the total cost of ownership of hydrogen fuel cell, battery-electric and internal combustion engine vehicles found that in 2021, several fuel cell vehicles were cost competitive with thermal engine vehicles, but not with BEVs, which are expected to remain the lowest in cost until at least 2050.
On almost all aspects, the business case for battery-electric vehicles is stronger than that of hydrogen fuel cell vehicles. And yet, S&P Global predicts that there could be 13 million fuel cell vehicles in operation by 2030 as the cost of green hydrogen production drops below US$3 per kg.
Hydrogen vs batteries: supply chain considerations
Beyond its promising applications for heavy-duty transportation, shipping and even aviation, green hydrogen presents significant advantages in terms of supply chains.
Batteries require scarce minerals such as lithium, cobalt and nickel, and the race to produce enough of these to meet the needs of an electrified world is leading causing environmental and human rights concerns in resource-rich countries like the Democratic Republic of the Congo (DRC), Chile and Bolivia.
Car batteries also have a short lifespan of about three to five years, resulting in large amounts of potentially toxic waste if not recycled.
In comparison, fuel cells are made of more common materials like aluminium, platinum and stainless steel, and hydrogen-fuelled vehicles have been found to have a similar lifespan to conventional cars – between 190,000 and 300,000 km.
So while at the organisational level, it is likely more advantageous to invest in battery-electric vehicles at this stage, it is also worth following in Amazon’s footsteps, even at a much smaller scale, and considering how to get involved in hydrogen too: it’s clear that both will have a place in our decarbonised future.
Member discussion