Scania’s green steel deal shows it trucking upstream on sustainability
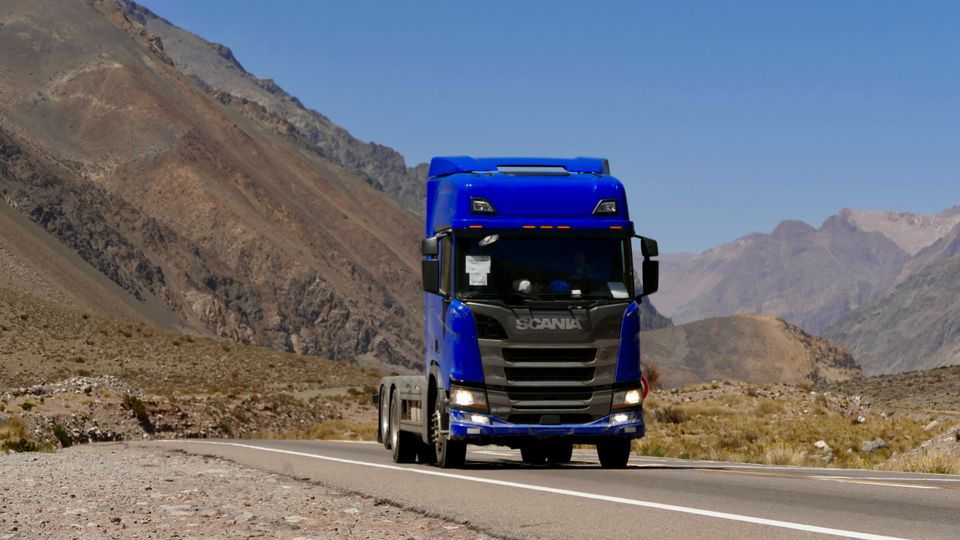
Scania, one of the world’s biggest heavy commercial vehicle makers, says it intends to only source “carbon-free” steel from its largest supplier, SSAB, by 2030.
Scania, which has delivered over 64,283 trucks to customers so far in 2023, has also already placed orders for “green steel” from supplier H2 Green Steel.
Its new agreement with global steel company SSAB will see it start buying steel made through a process that uses green hydrogen instead of coal to smelt down iron ore from 2026. From then, Scania expects to ramp up deliveries in order to make all of its trucks with this green steel by 2030 (initially only those made in Europe, with a view to extend this commitment to China and Latin America production).
Scania Chief Sustainability Officer Andreas Follér said the agreement came after the company turned its attention to the carbon emission from its supply chain as it began a strategy of electrification.
“When we are transitioning from [internal combustion engines] to zero emission tailpipe vehicles - the main environmental impacts shift from downstream to upstream. From customer operations to supply chain,” he said, adding that battery cells, steel, aluminium and cast iron were identified as “hotspots” accounting for approximately 80% of upstream emission.
“We agreed to use our purchasing power to support the shift towards low-carbon solutions in these supply chains, and in 2022 we communicated the specification of our demands in a 2025 and 2030 perspective,” he said today.
The deal with SSAB is meant to send a demand signal to iron ore miners to step up their own processes’ decarbonisation, and to green hydrogen producers to increase output. Scania and SSAB are both part of the First Movers Coalition, which aims to accelerate the use of decarbonisation technologies for “hard-to-abate” sectors – and Scania CEO Christian Levin has claimed the company is “taking huge steps towards decarbonising our value chain by focusing on the raw materials that are especially carbon-intensive to produce.”
Scania is also in a partnership with Northvolt to accelerate the commercialisation of green battery cell technology derived from recycled batteries.
Accelerating steel decarbonisation
According to the latest State of Climate Action report, this acceleration is crucial if we are to meet the goals of the Paris Agreement. The carbon intensity of steel production currently remains around 1,890 kg of CO2 per tonne of crude steel.
To limit the temperature rise to 1.5ºC, this should go down to about 1,340 kg, but only a third of the world’s top 50 steel producers have set net zero targets.
“Not all industrial processes can be easily electrified, and new solutions will likely be needed to reduce GHG emissions from chemical reactions and high-heat industrial processes, particularly for steel and cement,” note the report’s authors.
State of Climate Action, published today by Systems Change Lab, also hails the development of new production processes that replace coking coal with green hydrogen – yet according to the Green Steel Tracker, planned capacity for coal-based blast furnaces still surpasses planned green iron and steel capacity by a factor of 2.5.
Scania Chief Sustainability Officer on decarbonising the value chain
Scania’s CSO said the green steel journey had started with questions around the sustainability impacts of battery-electric trucks made from non-decarbonised materials using polluting processes and energy sources.
To get to the bottom of the issue, the company conducted a life cycle analysis of battery-electric trucks in 2021, which found that their production entails a higher environmental impact than that of internal combustion engine (ICE) trucks, “mainly due to energy-intensive battery cell manufacturing”.
At the moment, more than 90% of Scania’s 134 million tonnes of Scope 3 emissions come from customers driving the trucks, so switching to battery-electric would still result in significant emissions reductions of 38% to 63% – but it will also shift the company’s value chain emissions from product use to upstream materials.
“Stay tuned for our next chapter as we are working our way towards a sustainable automotive supply chain,” Follér added.
Member discussion