Rio Tinto joins consortium on EU-funded green steel project
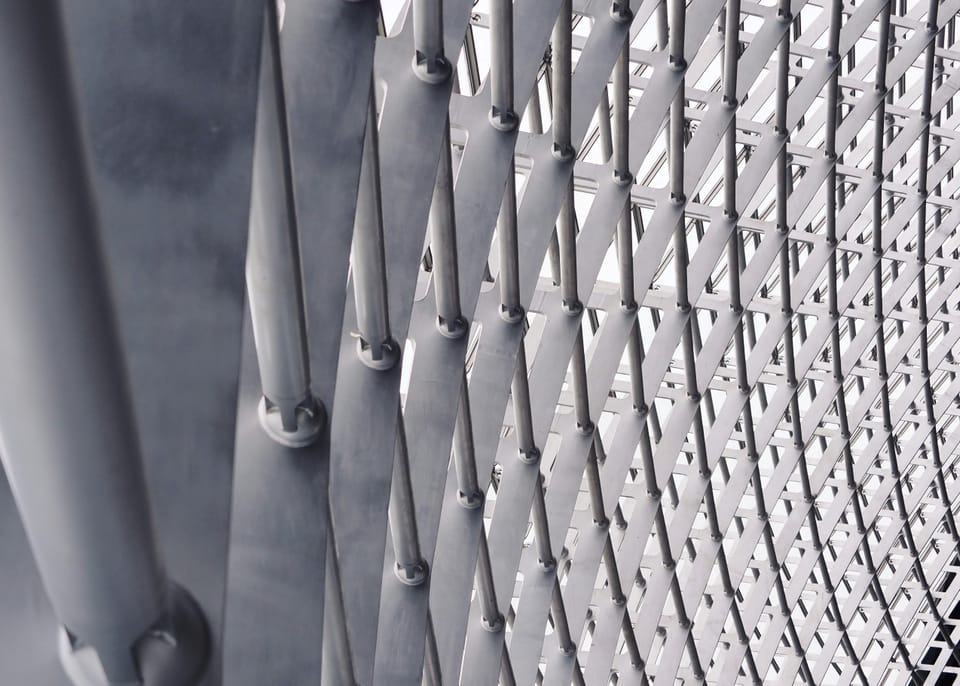
Global mining firm Rio Tinto will provide 70% of the iron ore used at an industrial-scale green steel prototype plant in Austria, as part of an agreement to support the development of low-carbon steelmaking.
Rio Tinto joins engineering firm Primetals Technologies, energy giant Mitsubishi Corporation, as well as voestalpine in this green steel consortium, which has received funding from the EU and the Austrian government.
The prototype plant, located in Linz, Austria, is expected to start producing hot briquetted iron, hot metal, and pig iron in 2027, using an innovative process called hydrogen-based fine-ore reduction (HYFOR). HYFOR reduces the carbon footprint of steelmaking by eliminating the need to pre-process iron ore into pellets and using hydrogen as a reduction gas.
The Linz plant will be the first hydrogen-based direct reduction plant linked to a renewable-powered smelter, allowing it to produce a projected three tonnes of hot metal per hour.
“This project represents a significant advancement in future-proof ironmaking – for the first time, we will implement a continuous production process with hydrogen-based direct reduction,” said Alexander Fleischanderl, Chief Technology Officer and Head of Green Steel at Primetals Technologies.
Rio Tinto as the main iron ore supplier
As part of the agreement, Rio Tinto will supply 70% of the iron ore to be used in the new plant. It will also support Primetals Technologies to accelerate the commercialisation of the technology.
Rio Tinto General Manager, Steel Decarbonisation Thomas Apffel said: “We are delighted to join a consortium that encompasses the entire iron and steelmaking value chain. By contributing our ironmaking expertise and iron ores from our Pilbara, Iron Ore Company of Canada, and future Simandou operations, we aim to advance the development and adoption of fluidised bed technology. This fines-based ironmaking solution presents a compelling alternative to shaft furnace technology by eliminating the need for pelletisation, potentially offering substantial benefits to both steelmakers and miners. Rio Tinto welcomes additional participants to the consortium and looks forward to supporting the widespread implementation of this innovative technology.”
Accelerating green steel
Traditional steelmaking uses coal as a reducing agent, making steel one of the most carbon-intensive industries in the world. The carbon intensity of steel production currently stands around 1,890 kg of CO2 per tonne of crude steel – yet to meet the goals of the Paris Agreement, it should be lowered to about 1,340 kg.
Innovative technologies like the one in this prototype plant are showing promise, with steel buyers sending strong demand signals: truckmaker Scania, for example, is aiming to only purchase ‘carbon-free’ steel from its main supplier SSAB by 2030.
Since 2021, Primetals Technologies has operated a pilot plant on voestalpine’s premises in Donawitz, Austria, and has run numerous successful test campaigns, but the Linz plant is the first industrial-scale operation.
“Mining and trading of ferrous raw materials has been one of our core businesses for many decades and we envision to develop a new supply of low emission metallics to support steel decarbonisation,” said Kenichiro Tauchi, COO, Ferrous Raw Materials Division of Mitsubishi Corporation.
Member discussion