Jaguar Land Rover generates £100mn from circularity initiatives
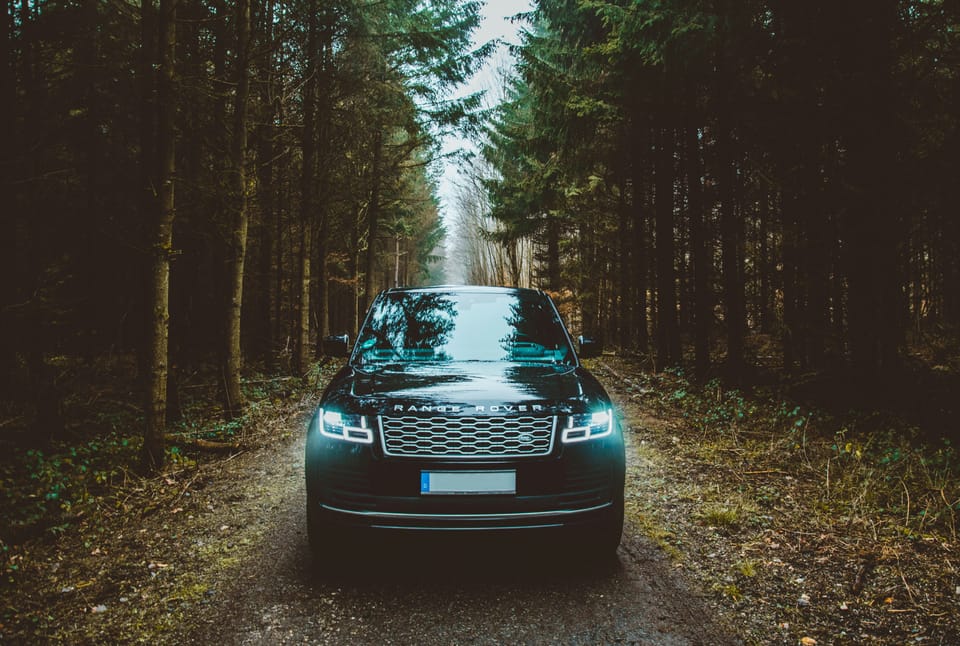
Luxury carmaker Jaguar Land Rover (JLR) says it has generated over £100 million of value by reusing, refurbishing, repurposing and recycling tools and equipment instead of buying them new.
The company is focusing on circularity as it prepares its operations for the production of fully electric cars. By using circular kit – from entire production lines to screwdrivers – robots and scrapped metal, JLR is saving millions of pounds and reducing its carbon footprint.
The company has reused over 50,000 square meters of kit from its Castle Bromwich site, which ceased production last year, as well as from the Electric Propulsion Manufacturing Centre (EPMC) in Wolverhampton and Graz, Austria. This equipment was redeployed across production sites in the UK and Slovakia.
Hundreds of second‑life robots have also been installed at Solihull, Halewood, and the EPMC in Wolverhampton to support the production of JLR’s next-generation electric vehicles and battery packs.
In addition, 18,600 tonnes of scrapped metal from Castle Bromwich and Graz have been sent to a supplier for recycling, with the resulting steel emitting 1.2 tonnes less CO2e per tonne, compared to steel made from virgin metal.
JLR CSO: ‘Sustainable choices are not always more expensive’
“As we are entering a critical phase in our electrification journey, JLR has at heart and aims to act as a responsible user of resources by enhancing product utility and longevity, and maximising recycling and repurposing.
“It’s not only the right thing to do, but it also improves profitability and increases supply chain resilience. Through these initiatives, JLR advocates that sustainable choices are not always more expensive, they can help reduce costs and even become opportunities for the growth and development of our colleagues,” said JLR Chief Sustainability Officer Andrea Debbane.
The company aims to offer all its models in an electric version by the end of 2030, and achieve net zero by 2039. Upgrading industrial operations is a crucial part of this year’s plan as it prepares to launch an electric Range Rover – its popular SUV model.
Digital lifecycle management
After promoting Debbane to Chief Sustainability Officer last October, JLR created a broad cross‑functional group with members from industrial operations through to vehicle programmes – working across sites and technologies to identify asset reuse opportunities based on standard compliance, availability of spare parts, cost of refurbishment and servicing, potential scrap and sale revenues.
The company also focused on training its teams on technical, maintenance and safety skills, to be able to add the refurbishment and recalibration of tools to production standards on site.
In addition, a new digital management system has been developed in‑house, aiming to manage the life of every vehicle programme asset from acquisition through to sale, scrapping and reuse. The solution will soon include an internal marketplace where different JLR sites can purchase used assets.
Read also: Renault Group seeks 90% lower lifecycle emissions with new model
Member discussion