Carbon costs and rising green steel demand justify €4.5 billion mill investment for SSAB
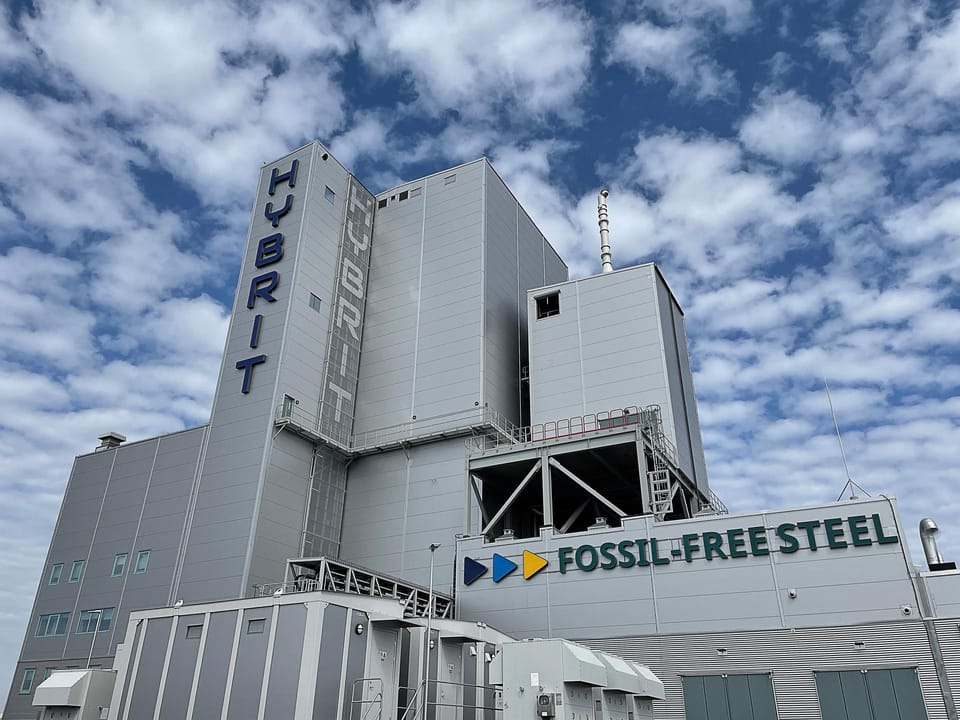
Swedish company SSAB is investing €4.5 billion in a new mill that is expected to produce 2.5 million tonnes of fossil-free steel a year – a sign that carbon costs and rising green steel demand are strengthening the business case for large capital investments.
The company expects this investment to result in “significant value creation”, as demand for green steel is rising. As an example, truck maker Scania, which sources most of its steel from SSAB, signed a deal with the supplier to purchase only “carbon-free” steel from 2030 onwards.
At current commodity forecasts, lower fixed costs, higher efficiency, shorter lead times and the elimination of rising carbon costs incurred under the EU’s Emissions Trading System (EU ETS) should improve the site’s annual earnings before tax (EBITDA) by more than €430 million (SEK 5 billion), the company notes.
Set to begin operations by 2029, the new facility will replace SSAB’s current blast furnace mill in Luleå and expand production capacity by 0.5 million tonnes a year. It will include two electric arc furnaces, a direct strip rolling mill to produce specialty products, and a cold rolling complex to serve the company’s mobility segment (including clients like Scania), with a broader offering of premium products.
SSAB fossil-free mill to cut Sweden’s emissions by 7%
Moving steel production from Luleå’s blast furnace mill to the new fossil-free mill is set to reduce Sweden’s carbon emissions by 7%. This is in addition to the 3% cut expected to be achieved through a similar mill conversion at Oxelösund, which SSAB announced in 2023.
These facility developments build on a pilot project launched in 2016 by SSAB, LKAB and Vattenfall, known as the HYBRIT initiative: there, the three companies invested in a pilot plant to convert iron ore into sponge iron using green hydrogen, with LKAB producing the sponge iron, Vattenfall producing the fossil-free energy and SSAB making fossil-free steel.
The sponge iron produced at HYBRIT is set to supply SSAB’s new fossil-free mills at both Oxelösund and Luleå, in addition to recycled scrap.
“The transformation of Luleå is a major step on our journey to fossil-free steel production. We will remove 7% of Sweden’s carbon dioxide emissions, strengthen our competitive position and safeguard jobs with the most cost-effective and sustainable strip production in Europe,” said SSAB’s President and CEO Martin Lindqvist.
Decarbonising the steel industry
The carbon intensity of steel production currently remains around 1,890 kg of CO2 per tonne of crude steel, according to the latest State of Climate Action report. To limit the temperature rise to 1.5ºC, this should go down to about 1,340 kg.
The development of new production processes that replace coking coal with green hydrogen, as is the case in the HYBRIT initiative, is expected to accelerate the sector’s decarbonisation, but in 2023, planned capacity for coal-based blast furnaces still surpassed planned green iron and steel capacity by a factor of 2.5.
“Together with our partner LKAB we are making a commitment to eliminate the CO2 emissions from our value chain and establish the new benchmark technology for a fossil-free future. In the process we are also safeguarding Nordic industrial competitiveness for decades to come, and supporting the thousands of customers that rely on quality steel from our value chain,” addedLindqvist.
Member discussion